Manufacturing concerns are rising, in large part due to increased costs of supply, raw materials, and imports. As such, any business running a supply line is likely to be looking at what, precisely, they can do to cut costs in their business without cutting operational capacity. Here, we’re going to look at how creating a smaller, leaner, and more streamlined manufacturing process might be the answer. The tips below might help you find the fat that you can trim while finding cost-effective ways to meet essential needs.
Accurately forecast your production
It’s important, in manufacturing, to have a reasonable expectation of how many products you are able to produce in any given time frame. However, if you haven’t taken the time to ensure accurate forecasting, this can be difficult. You need the right systems in place to be able to tell how long the manufacturing process takes, and how much output you can expect in each day. This can be done in part through the analysis of past data, i.e., your past results, but there are also forecasting techniques like statistical modelling, which look at things like your inventory management, resource allocation, and production schedule to help you put together the best estimate of what you output is going to be within any period of time.
Know how to measure the effectiveness of change
Before you start making too many changes to your production line, you want to get a good idea of whether or not they are going to work. Prediction is all well and good, but measurement is what you really want to focus on. Take the time to research and define manufacturing key performance indicators. You want to know what to track, and what changes influence which KPIs. You don’t need to track every possible analytic and metric available, you want to focus on those that really make a significant difference on your bottom line. Getting too bogged down in the details can waste valuable manhours.
Find where waste is being created
Just as your KPIs can you measure the effectiveness of your production line before and after you make changes to it, taking the time to identify the major sources of waste on your line can also help you ensure that your energy is being spent where it is most effective. You can measure waste in time or in materials, analysing how much is spent needlessly across the board, be it through product loss and errors, downtime, staff mistakes, and more When you have a better idea of where this loss is occurring, then you know what you have to fix, first. This will stop you from focusing on changes that might seem important, but won’t really make that much of a difference at the end of the day.
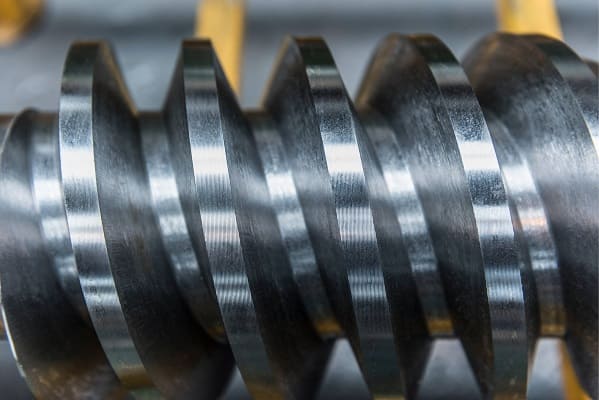
Monty Rakusen / Avalon
Declutter your workspaces
One of the things that can really slow the physical processes of working in a production line is the presence of clutter. Materials, waste, unused machinery, and other things that take up space unnecessarily can force your workers and materials to travel further to reach the things that they need and can reduce the amount of space available for your workers to use. What’s more, clutter and mess also increase the risk of accidents and injuries greatly, such as slips, trips, and falls. Take the time to go over your manufacturing space, to identify any clutter, and to make sure that it is either cleaned up, stored away, put in its right place, or thrown out if it has no place there. It will create a much more productive and motivated environment.
Ensure standards of best practices and quality
If you’re experiencing loss due to errors and problems in the finalised products, then one of the best ways to prevent that is to ensure that your team is operating to the right standards. For instance, take the approach of best practices when implementing manufacturing processes, focusing on quality throughout the process, communicating between teams, and minimising waste through a quality program. Quality programs set the standards that workers have to follow to ensure that manufacturing processes use only the materials that they need, within a reasonable time frame and realistic but manageable loss expectations.
Look for bottlenecks
One of the biggest causes of lost time in most manufacturing processes is the existence of bottlenecks. Bottlenecks are parts of the process in which no other work can progress until that process is done. As such, you might have several production steps running concurrently, but when they reach that bottleneck, they need to get through that process before things can open up again, slowing your output considerably. There are various ways to address bottlenecks. For instance, if you’re waiting for the work of one machine to help products get to the next part of the manufacturing process, buying a second machine that does the same thing can have more products getting through it at once. There are multiple types of bottlenecks, of course, so it’s worth taking the time to see which is most likely affecting your production line.
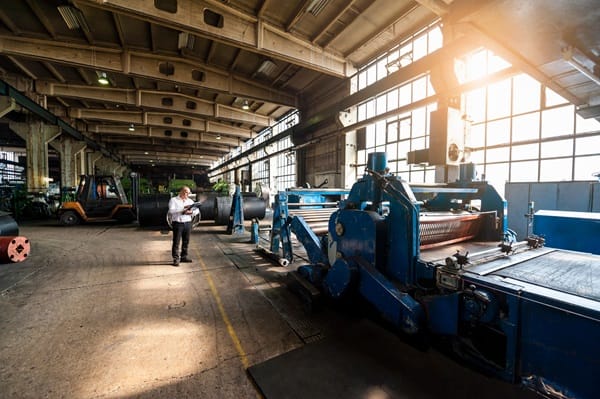
Daniel Ingold / Avalon
Work with other manufacturing services
If you’re looking to incorporate new production processes into your manufacturing line, then you have to address the major costs that can come with it. New machinery, professionals equipped to handle them, and the reconfiguration of your existing manufacturing line can all be very expensive. It may, instead, be cheaper to outsource the production or provision of certain components to third parties. For instance, if you’re working with metal products, it may be a lot less costly to work with rubber strip manufacturers to secure and seal your own products, rather than to try and start producing them, yourself. If your business is able to eventually grow to the point that it could internalise those processes, that’s ideal, but trying to build it internally from the get-go can come with very high initial costs.
Automating where possible
Although it has been something of a contentious subject, given that it does put the jobs of workers at right, automation is becoming a necessity for many manufacturers to survive and find a profit. Automation, simply put, offers one of the most efficient ways to boost your production line. You can reduce your need for physical labour and the costs that come with it, while also diminishing the role that human error plays in levels of loss throughout the production line. You still need experienced operators to ensure the smooth workflow of automated machinery and processes, as well as to ensure that any output from automated processes reaches the demanded levels of quality.
Invest in better machinery
Of course, sometimes, a bigger initial expense is worth it to cut your running costs significantly. If you have spotted new manufacturing machinery on the market that is significantly better than yours, more efficient, more accurate, and less prone to errors, then investing in it could end up greatly reducing the costs accrued through loss and work interruptions. You can make new machinery a lot less expensive by opting for used and second-hand manufacturing equipment, as well. Don’t forget to sell any machines that you’re not using to help cover part of the budget, as well. Track the cost of a new machine with the decrease in losses through the coming months to see how quickly your investment pays off.
Rely on lean principles
The lean principles have been widely adopted not just throughout the manufacturing landscape, but into the world beyond. This is because they work. Lean manufacturing is a continuous process of identifying the sources of waste and loss and taking steps to improve the value of every aspect of your production line. It incorporates organisation, maintenance, and efficiency, creating a flow in your workplace that can see you operating a lot more smoothly. It’s not difficult to learn the lean principles yourself and to start incorporating them in your own business, although there are plenty of agencies that will help look over your existing setup to see how you can better incorporate it, too.
Plan with the right software
Manufacturing processes can sometimes seem difficult to plan from a bird’s eye view because they can rely on many different factors, including machine operation, staffing, inventory availability, maintenance schedules, and much more. Traditional small business approaches may not be enough to effectively plan for manufacturing concerns, even if the production line isn’t that big. This is where enterprise resource planning, also known as business management software, can come in. This software is designed to take multi-faceted business operations and to create a system that can overlook all of them, and how they interact and rely on one another, to help spot issues that might be happening in one sector, slowing things down in other sectors.
Manufacturing is a costly process that is getting more and more costly. Hopefully, the tips above will help you find a way to cut the costs of your own setup, allowing you to keep producing the goods you need for the foreseeable.
Leave a Comment